Custom Silicone Medical Parts for Diagnostic Equipment
Custom Silicone Medical Parts for Diagnostic Equipment
In the rapidly evolving field of medical diagnostics, the demand for high-precision, reliable, and biocompatible components has never been greater. Custom silicone medical parts play a pivotal role in ensuring the accuracy, safety, and longevity of diagnostic equipment. As a leading manufacturer specializing in custom silicone solutions, we provide tailored, high-quality silicone components designed specifically for the rigorous demands of medical diagnostics.
The Critical Role of Silicone in Diagnostic Medical Equipment
Silicone's unique properties make it an ideal material for medical applications, especially in diagnostic devices where sterility, flexibility, and durability are paramount. Silicone offers excellent chemical stability, biocompatibility, temperature resistance, and flexibility, making it indispensable for components such as seals, gaskets, diaphragms, connectors, and tubing.
Custom Silicone Solutions for Diagnostic Equipment: Our Expertise
Our company specializes in designing and manufacturing bespoke silicone parts tailored to meet the precise specifications of diagnostic equipment manufacturers. Our state-of-the-art production facilities utilize advanced molding techniques such as compression molding, injection molding, and liquid silicone rubber (LSR) molding to produce high-precision components.
Key Types of Custom Silicone Parts We Provide
Component Type | Application in Diagnostic Equipment | Material Properties |
---|---|---|
Silicone Seals & Gaskets | Prevent fluid leaks, maintain airtight conditions | High elasticity, chemical resistance |
Diaphragms | Control fluid flow, pressure regulation | Flexibility, fatigue resistance |
Connectors & Fittings | Ensure secure, sterile connections between devices | Precise tolerances, biocompatibility |
Tubing & Hoses | Transport fluids, gases within diagnostic systems | Flexibility, durability, sterilization compatibility |
Sensor Encapsulation | Protect sensitive electronics from fluids and contaminants | Electrical insulation, chemical stability |
Designing Custom Silicone Components for Diagnostic Precision
Our design process emphasizes collaborative development, ensuring that each silicone part aligns with strict industry standards and specific client requirements. We utilize advanced CAD modeling and finite element analysis (FEA) to optimize performance, durability, and manufacturability.
Key Considerations in Custom Silicone Part Design
- Dimensional Accuracy: Achieving tight tolerances for seamless integration with other components.
- Material Selection: Choosing the appropriate silicone grade based on chemical exposure, sterilization method, and mechanical demands.
- Surface Finish: Ensuring smooth surfaces to prevent contamination and facilitate cleaning.
- Sterilization Compatibility: Designing parts that withstand autoclaving, EtO sterilization, or gamma irradiation.
Manufacturing Excellence: Ensuring Quality and Consistency
Our manufacturing process adheres to ISO 13485 standards, guaranteeing quality management in medical device production. We employ cleanroom environments for sensitive components, minimizing contamination risks.
Advanced Manufacturing Techniques
- Liquid Silicone Rubber (LSR) Molding: Enables high-volume production of complex, precise parts with excellent surface quality.
- Injection Molding: Suitable for large-scale production of intricate components with consistent tolerances.
- Prototype Development: Rapid prototyping services allow clients to test and refine designs before mass production.
Advantages of Our Custom Silicone Parts in Diagnostic Devices
- Enhanced Accuracy: Precisely manufactured components ensure reliable diagnostics, minimizing errors.
- Improved Safety: Biocompatible and sterilizable parts reduce infection risks.
- Operational Longevity: Resistant to wear and chemical degradation, leading to cost savings.
- Design Flexibility: Custom shapes, sizes, and features tailored to specific device requirements.
- Regulatory Compliance: Meeting medical device standards globally, facilitating market approval.
Applications of Custom Silicone Medical Parts in Diagnostic Equipment
Our silicone components are integral to a broad spectrum of diagnostic instruments, including:
- Immunoassay systems
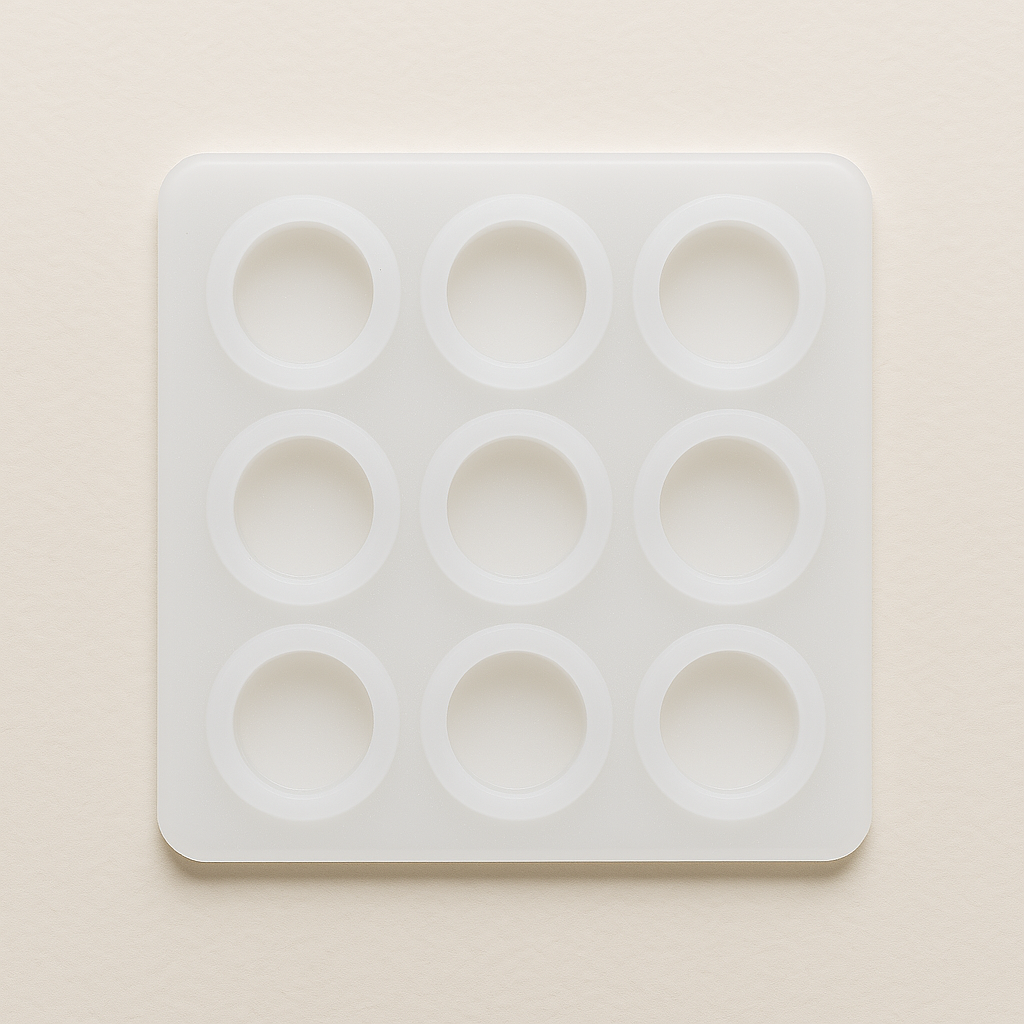
- Molecular diagnostic platforms
- Imaging devices
- Point-of-care testing units
These applications demand precise, reliable, and sterile components, which we consistently deliver.
Case Study: Enhancing Diagnostic Device Performance with Custom Silicone Diaphragms
A leading manufacturer of blood analyzers approached us to develop custom silicone diaphragms that could withstand multiple sterilization cycles while maintaining elasticity and sealing integrity. Our team designed a high-precision diaphragm using medical-grade LSR, ensuring perfect fit and long-term durability.
Results:
- Improved device accuracy due to enhanced sealing.
- Reduced maintenance costs owing to increased component lifespan.
- Compliance with international standards for medical devices.
Partnering for Success: Why Choose Us for Custom Silicone Medical Parts?
- Expertise in Medical Silicone Manufacturing: Decades of experience serving the healthcare industry.
- Customized Solutions: From initial design to final production, tailored to your specifications.
- Regulatory Knowledge: Guidance to ensure compliance with FDA, CE, ISO 13485, and other standards.
- Rapid Turnaround: Efficient processes for prototyping and mass production.
- Global Supply Chain: Reliable delivery worldwide, ensuring your production timelines are met.
Conclusion: Elevating Diagnostic Equipment with Custom Silicone Components
In the cutting-edge realm of medical diagnostics, custom silicone parts are not just components—they are critical enablers of precision, safety, and longevity. Our commitment to quality, innovation, and customer satisfaction positions us as your trusted partner in developing high-performance silicone solutions that elevate your diagnostic devices to new standards of excellence.
Contact Us Today for Custom Silicone Medical Parts
Partner with us to transform your diagnostic equipment with custom-engineered silicone components that meet the highest industry standards. Contact our team for consultation, prototype development, or large-scale manufacturing.