How to Choose a Silicone Plastic Overmolding Manufacturer?
Choosing the right silicone plastic overmolding manufacturer can be confusing. I have been there before.
To choose a silicone plastic overmolding manufacturer, focus on their technical expertise, material quality, and ability to customize solutions for your industry needs.Let me share the key questions I asked myself before finally finding the right partner for my project.
[Table of contents]
What is the best plastic for overmolding?
Can silicone be overmolded?
What is the best silicone for molding?
What are the methods of manufacturing silicone?
What is the best plastic for overmolding?
Picking the right plastic is the first step to ensure overmolding success.
The best plastics for overmolding are often thermoplastic elastomers (TPE), polypropylene (PP), and polycarbonate (PC) because of their flexibility and bonding strength.
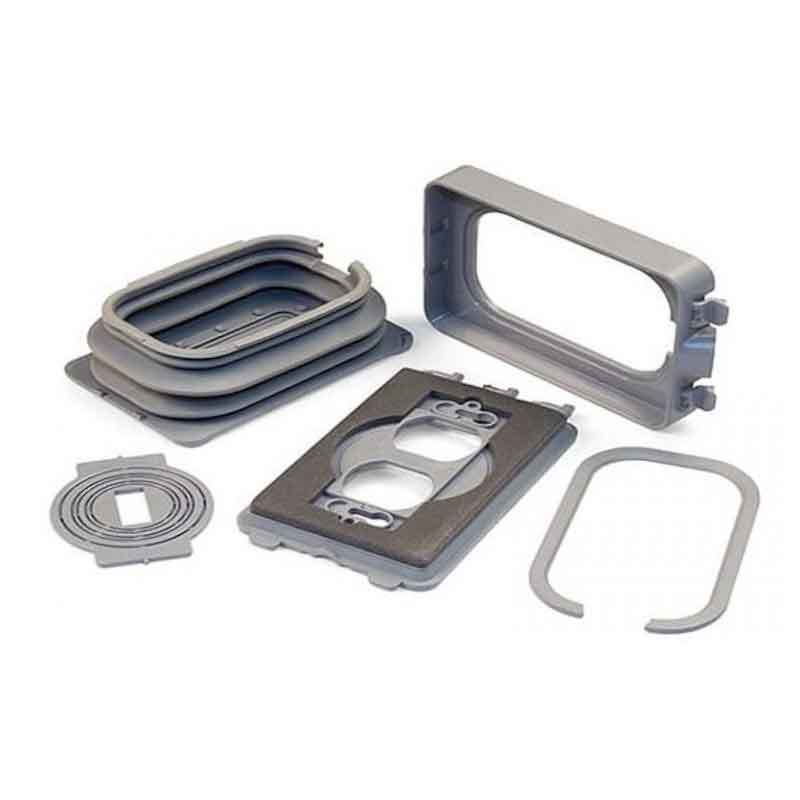
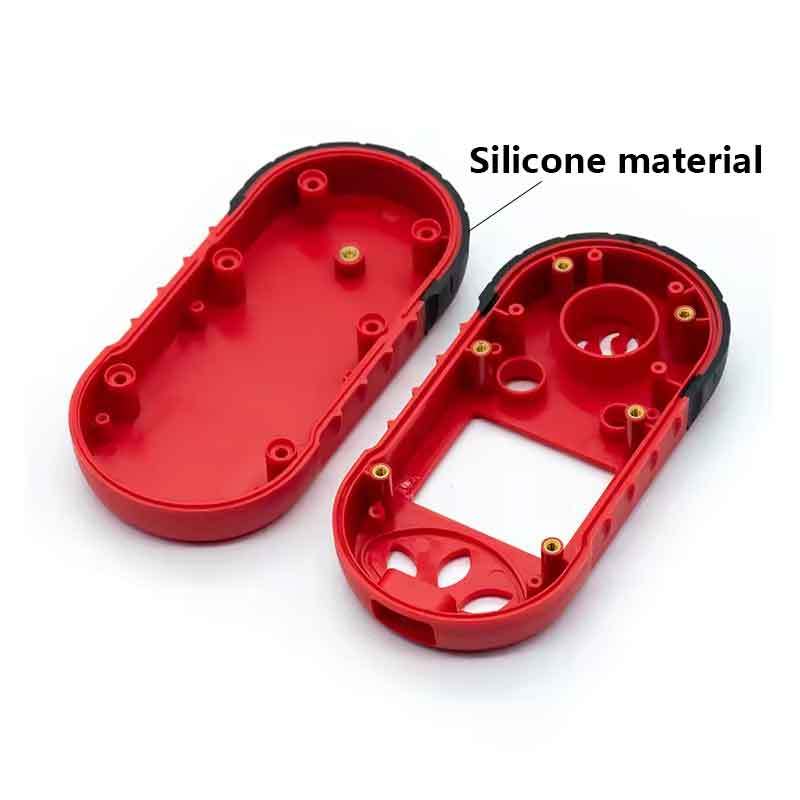
Why TPE is Popular for Overmolding
TPE offers a soft touch feel and great adhesion to many substrates. It is often used in consumer products like toothbrushes and phone cases.
Plastic Type | Features | Best Use Case |
TPE | Flexible, strong bond | Consumer electronics |
PP | Lightweight, chemical resistant | Automotive parts |
PC | High impact strength | Medical devices |
Key Factors When Choosing Plastic
1.Compatibility: Not all plastics bond well with silicone.
2.Durability: Must withstand temperature changes.
3.Flexibility: Should fit product design needs.
Can silicone be overmolded?
I used to think silicone could only be molded alone. I was wrong.
Yes, silicone can be overmolded onto various substrates like metals, plastics, and even fabrics with the right surface treatment and technology.
How Silicone Overmolding Works
Silicone overmolding usually involves:
Surface preparation like plasma treatment.
Injection molding or compression molding.
Curing under controlled temperatures.
Common Applications of Silicone Overmolding
Waterproof seals for electronics
Medical device housings
Automotive gaskets
Silicone's natural flexibility and biocompatibility make it perfect for critical industries. Learn more about silicone overmolding advantages.
What is the best silicone for molding?
Choosing the right silicone grade was a game-changer for my project.
Liquid Silicone Rubber (LSR) is considered the best material for silicone molding due to its high precision, durability, and ability to mold complex parts.
Why LSR Stands Out
Low viscosity: Easy to inject into fine details.
Heat resistance: Withstands up to 200°C or more.
Biocompatibility: Safe for medical and baby products.
Silicone Type | Advantages | Common Use |
LSR | High precision, fast curing | Medical devices, electronics |
HTV Silicone | High strength, requires high heat to cure | Automotive parts |
Important Tips for Selecting Silicone?
Match curing process with production needs.
Check certifications for medical or food-grade applications.
Evaluate the mechanical properties.
What are the methods of manufacturing silicone?
At first, I thought silicone was just "mold and done." Turns out, there is more to it.Silicone manufacturing methods include injection molding, compression molding, extrusion, and liquid injection molding, each suited to different product types.
Major Silicone Manufacturing Processes
Injection Molding
Ideal for high-volume production. LSR is injected into closed molds and cured quickly.
Compression Molding
Used for larger, simple parts. Silicone is manually placed in a heated mold.
Extrusion
Creates continuous silicone profiles like tubes and rods.
Liquid Injection Molding (LIM)
Highly automated, perfect for precise, complex components.
Method | Best for | Key Benefit |
Injection Molding | Mass production | High precision |
Compression Molding | Simple shapes | Lower tooling cost |
Extrusion | Tubes, rods | Continuous production |
LIM | Complex designs | High automation |
Conclusion
Choosing the right silicone plastic overmolding partner starts with understanding materials and methods.